Ochrona PCB z użyciem soldermasek – część 3
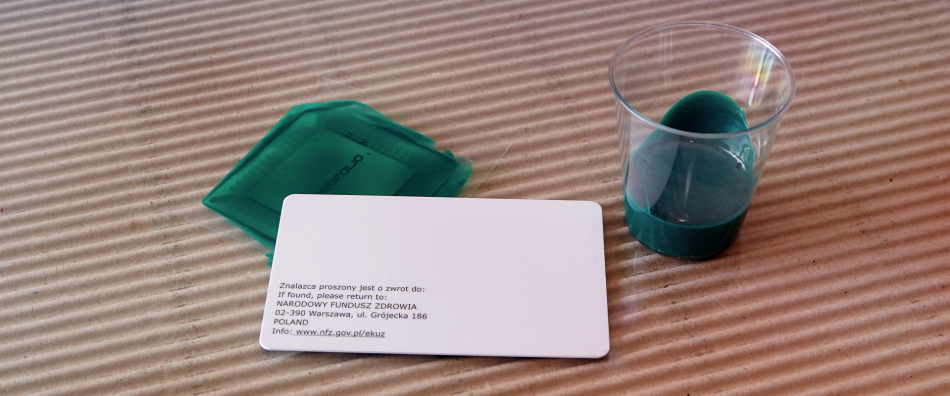
W dzisiejszym artykule chciałbym wam przestawić kilka metod z jakimi możemy mieć do czynienia w przypadku produktu jakim jest soldermaska UV. Dostępne na rynku Soldermaski UV to preparaty jednoskładnikowe, które pod wpływem światła ultrafioletowego ulegają utwardzeniu. W przemysłowych zastosowaniach maski te nanoszone są za pomocą sitodruku, pomysłowość hobbystów sprawiła jednak, że w domowych zastosowaniach procesy ich nakładania dość znacznie odbiegają od pierwotnych założeń producenta.
Soldermaska UV rozprowadzana pod folią
Gdy zakupy na ebay'u u zagranicznych kontrahentów oraz zakupy "u chińczyka" (np: AliExpress) stały się popularniejsze, na polski rynek powoli zaczęła napływać stosunkowo niedroga soldermaska reperacyjna UV (przy zakupie 100 gram należy się spodziewać ceny rzędu 35pln, przy zakupie 10 mililitrowej strzykawki cena rośnie do 15 złotych). Ta jednoskładnikowa farba zasadniczo przeznaczona jest do nakładania metodą pełnego sitodruku jednak w domowym zaciszu typowo rozprowadzana jest na płytce drukowanej w mniej konwencjonalny sposób. Proces w tej metodzie rozpoczynamy od nałożenia pewnej ilości farby na płytkę drukowaną by następnie docisnąć wszystko przeźroczystą folią. Farba ma konsystencję gęstego majonezu i jej równomierne rozprowadzenie pod folią wymaga czasu i siły, dlatego też w zabiegu tym najlepiej pomóc sobię miękką ściereczką, wałkiem gumowym lub kawałkiem plastiku z równą krawędzią (np: nieważną kartą kredytową). Gdy farba pod folią jest już rozprowadzona, przykładamy folię z mozaiką punktów lutowniczych i naświetlamy promieniami UV, w zależnosci od mocy lamp od kilku do kilkanastu minut. Po naświetleniu zrywamy folię, która miała bezpośredni kontakt z płytką, a następnie zmywamy pozostałości nieutwardzonej farby za pomocą rekomendowanego rozpuszczalnika (aceton lub benzyna).
Bez wątpienia do zalet metody należy zaliczyć jej prostotę. Wydajność, wg zapewnień dystrybutora 100g farby powinno wystarczyć na około 15 płytek dwustronnych formatu A4, zważywszy jednak na grubość połoki jaką jesteśmy w ten sposób nanieść, bardziej realną wielkością jest 4-5 płytek dwustronnych formatu A4, co stanowi nieco lepszy wynik niż w przypadku farb do szkła. Jako że w procesie wykorzystana jest soldermaska UV, w teorii możemy spodziewać się całkiem dobrych własności elektrycznych oraz mechanicznych (choć nie tak dobrych jak soldermasek przeznaczonych do wypalania). W praktyce, ze względu na "kombinowany" sposób nakładania tej farby na powierzchnię płytki, nie możemy jednak liczyć na parametry jakie podaje producent, a dodatkowo zetkniemy się z pewnymi wadami.
W pierwszej kolejności należy wskazać na problem powietrza jakie zostaje uwięzione pod nieprzepuszczalną folią. Estetyka płytki nie ucierpi jeśli uwięziony zostanie jedynie malutki pęcheżyk. Czasem jednak w gęstej farbie formują się płaskie i rozległe bąble, a te kwalifikują płytkę do rozpoczęcia całego procesu od nowa (nowa porcja farby i nowa folia). Im większa płytka tym trudniej zapanować nad powietrzem w pułapce z folii.
Bardzo istotną wadą tej metody jest nierównomierne rozłożenie powstającej powłoki. Co gorsza najwiekszą jej grubość otrzymamy w tych miejscach płytki, gdzie najmniej tego potrzebujemy. Wynika to bezpośrednio z technologii nakładania i niestety nic z tym nie zrobimy. Przyjrzyjmy się zatem mechanice powstawania tego problemu by zrozumieć jego istotę. Jak każdy wie, wytrawiona płytka drukowana którą poddaliśmy trawieniu to mozaika ścieżek miedzianych na laminacie szklanym. Tam gdzie miedź jest wytrawiona, powstają swoiste "doliny" a pozostała po trawieniu miedź tworzy wypłaszczone "góry" o wysokości od 17 do nawet 105 mikrometrów. Na granicy "gór" i "dolin" znajdują się oczywiście strome "urwiska". Gdy taką "rzeźbę terenu", zalewamy farbą, ta wypełnia po brzegi nasze "doliny" a na płaskich wierzchołkach "miedzianych gór" pozostaje jej naprawdę niewiele. Co więcej folia, pod którą rozprowadzamy farbę jest elastyczna i pod naciskiem zapada się w "dolinach" wypełnionych farbą, wywierając tym samym największy nacisk na krawędzie naszych miedzianych "urwisk". W efekcie na krawędziach ścieżek pozostaje znikoma ilość lakieru. Nie trzeba tłumaczyć, że w takiej sytuacji właściwości elektryczne powłoki budzą spore wątpliwości.
Kolejny problem wynika z obecności foli, pod którą rozprowadzana jest farba. Stanowi ona bowiem dodatkowy dystans pomiędzy folią maskujacą a powierzchnią płytki, co wywołuje tak zwany efekt paralaksy i naświetlenie obszarów, które powinny zostać nieutwardzone. W efekcie soldermaska sięga od kilku do kilkunastu milsów dalej niz powinna. Nie zaleca się również rozprowadzać farby bezpośrednio pod folią maskującą, ze względu utrudnione dopasowanie punktów lutowniczych do wzoru na kliszy.
- prostota procesu
- niewygórowana cena farby (około 35pln za 100ml)
- powstaje gładka szklista powłoka
- powłoka ma nierównomierną grubość
- podczas nanoszenia najwięcej farby gromadzi się pomiędzy ścieżkami, na ich wierzchu już zdecydowanie mniej, natomiast powłoka na granicach ścieżek jest zazwyczaj krytycznie mała, poodając w watpliwośc własności elektryczne powłoki
- jeśli nie zachowamy należytej staranności, powstająca powłoka będzie pokryta pęcheżykami powietrza
- połoka jest dość twarda jednak nadal podatna na zarysowania
- efekt paralaksy wynikajacy z obecnosci dodatkowej warstwy folii powoduje poszerzenie obszaru soldermaski
Soldermaska rozprowadzana pełnym sitodrukiem
Sitodruk polega na przeciskaniu farby, za pomocą tak zwanej rakli, przez gęstą siatkę na jakąś powierzchnię. Siatki wykonane są zazwyczaj z poliamidu lub poliestru i napięte są na aluminiowych lub drewnianych ramach.
Farbę możemy nakładać na materiał przez otwarte sito, co zapewnia 100% krycie powierzchni (sitodrukarze i poligrafowie takie krycie nazywają potocznie "nakładaniem apli"). Gdy wymagane jest selektywne pokrywanie materiału - a tak właśnie jest w przypadku tej metody, część oczek siatki sitodrukowej pokrywa się elastyczną emulsją maskujacą, a przeciskana farba przechodzi na materiał tylko tam gdzie oczka siatki pozostały otwarte.
Gdy chcemy przygotować płytykę drukowaną z dedykowanym dla niej wzorem maski lutowniczej, musimy odpowiednio wcześniej przygotować negatywowy wzór maski na sicie z użyciem dodatkowych preparatów i osprzętu. Najpierw specjalną rynienką nanosimy światłoczułą emulsję na całą powierzchnię siatki sitodrukowej i pozostawiamy do wyschnięcia w zaciemnionym pomieszczeniu, po czym naświetlamy ją przez kliszę pozytywową w specjalnych naświetlarkach z podsysaniem próżniowym a następnie wypłukujemy nienaświetloną emulsję za pomocą strumienia wody pod ciesnieniem, gotową siatkę z wzorem maskującym odstawiamy do wychnięcia. Dalszy etap nakładania soldemrmaski sprowadza się do zamocowania siatki nad powierzchnią płytki, w taki sposób by przygotowany wzór na sicie był spasowany z punktami lutowniczymi a następnie przeciśnięcie przygotowanej porcji farby jednym sprawnym ruchem rakli. W ostatnim etapie płytka drukowana z selektywnie naniesioną soldermaską wędruje pod lampy UV lub do pieca (w zależności od tego czy użyto farby UV czy farby termoutwardzalnej), gdzie następuje ostateczne jej utwardzenie.
Narzędzia takie jak rama sitodrukowa czy rakla to niewielki wydatek, a nanoszenie farby przez gotowe sito to dosłownie kilka sekund pracy. Ale jak się pewnie domyślacie "piętą Achillesową" tego procesu jest konieczność posiadania dodatkowego osprzętu i chemikaliów niezbędnych do przygotowania emulsji maskującej na czystej siatce. Nie bez znaczenia jest również czas, potrzebny do przygotowania takiej maski co sprawia, że na metodę tą decydują się głównie osoby lub zakłady produkcyjne, które chcą jednorazowo przygotować dość dużą serię identycznych płytek. Gdy rama sitodrukowa ma służyć do innych projektów, to dodatkowo musimy się zaopatrzyć w specjalne preparaty do usuwania z niej emulsji maskujacej (odwarstwiacze i otwieracze sita).
Ponieważ siatka sitodrukowa determinuje powstanie równej i jednakowo grubej powłoki w każdym miejscu gdzie została naniesiona, jakość finalnego produktu jest perfekcyjna. Zużycie farby w tej metodzie znacząco zależy od stopnia pokrycia płytki soldermaską oraz grubości emulsji maskującej na sicie. Przy założeniu stopnia pokrycia wynoszącego 90% i nanoszeniu farby przez prawidłowo wykonaną maskownicę ze 100 gram farby realnie możliwe jest wykonanie 6-7 płytek dwustronnych formatu A4. Koszt farby, jak już wspomnieliśmy przy okazji poprzedniej metody, rówież nie jest wygórowany. Trzeba się jednak liczyć z dodatkowymi wydatkami na szybko zużywające się materiały eksploatacyjne (wspomniana emulsja światłoczuła do wykonywania maski, odwarstwiacze i otwieracze sita).
- stosunkowo niska cena farby (około 35pln za 100ml)
- metoda daje bardzo dobre efekty wizualne
- powłoka jest jednorodna i równomiernie rozprowadzona po powierzchni płytki
- względnie dobra wydajność farby (6-7 dwustronych płytek formatu A4 ze 100gram)
- wysokie koszty eksploatacyjne zwiazane z regularnym zakupem emulsji do wykonywania maski i czyszczenia siatki z jej pozostałości rynienki do rozprowadzania emulsji oraz posiadanie odpowiednio duzych naświetlarek umożliwiających naświetlanie emulsji na sicie
- wyższe koszty ramy sitodrukowej - wynikające z konieczności stosowania droższych siatek kalandrowanych, eliminiujących efekt podświetlania podczas wywoływania emulsji na sicie
- proces mało elastyczny - by wykonać kilka pojedynczych płytek potrzebujemy dla każdej z nich osobnego wzornika na ramie, niejednokrotnie potrzebnych będzie kilka ram.
- konieczność zainwestowania odpowiednio duże naświetlarki UV, czy myjki ciśnieniowe do usuwania emulsji z sit
- duża czasochłonność procesu - ze względu na konieczność wykonywania dodatkowej powłoki na sicie, jej wykonanie i póżniejsze usuwanie
- rozdzielczość uzyskanego wzoru jest ściśle związana z parametrami siatki
Soldermaska UV - metoda kombinowana
W przypadku gdy solderaskę jaką dysponujemy jest soldermaska utwardzalna w promieniach UV, możemy pokusić się o zastosowanie metody kombinowanej, łączącej w sobie fragmenty wyjaśnionych do tej sposobów. Taka "kombinatoryka" eliminuje w pewnym stopniu niektóre wady powłoki ale niestety wprowadza kolejne. Żeby całkowicie wyczerpać wyczerpać temat dostępnych technik nakładania maski warto o niej wspomnieć.
Ponieważ rozprowadzanie farby pod elastyczną folią generuje znane już problemy, cienką i równomierną warstwę farby nakładamy metodą sitodruku przez otwarte sito, umożliwiając tym samym wydajność rzędu 10-11 płytek dwustronnych formatu A4 ze 100gram. Celowo nie używamy tutaj pędzla ani wałka, ponieważ gęste farby UV pochodzące z Hongkongu nie mogą być rozcieńczane a przez to możliwości ich nakładania w ten sposób są ograniczone. W kolejnym etapie do lekko podsuszonej warstwy farby przykładamy zwilżoną alkoholem kliszę z wzornikiem maski, po czym naświetlamy w promieniach UV przez kilka kilknaście minut. Po czym usuwamy folię i zmywamy nieutwardzoną promieniami UV farbę za pomocą rozpuszczalnika otrzymując gotową soldermaskę.
W teorii brzmi to doskonale, niestety wywołanie maski UV w racjonalnym czasie możliwe jest jedynie w warunkach beztlenowych. Przy dostępie tlenu proces naświetlania wymaga już 2-3 godzin. Cienką i miekką warstwę farby bardzo łatwo uszkodzić podczas nakładania i pasowania kliszy maskującej - co wymusi konieczność powtórzenia zabiegu od nowa. Gdy spróbujemy najpierw dobrze wysuszyć płytkę a dopiero później naświetlać ją pod kliszą zwilżoną alkoholem, próba zmycia nienaświetlonych obszarów zakończy się niepowodzeniem i cały obszar farby ulegnie utwardzeniu.
Choć metoda jest tania, szybka i nie wymaga dużych nakładów na osprzęt, to nakładanie soldermasek UV w ten sposób osobiście uważam za nieporozumienie, zwłaszcza w konfrontacji z takimi produktami jak soldermaski fotoobrazowe (o których napiszę za chwilę).
- stosunkowo niska cena farby (około 35pln za 100ml)
- duża wydajność
- farba po nałożeniu na PCB i następnie podsuszana, wykazuje opór podczas naświetlania i późniejszego wywoływania - wymagane są warunki beztlenowe
- podczas kontaktu plastycznej jeszcze farby z folią, bardzo łatwo może dojść do uszkodzenia cienkiej powłoki, mamy również do czynienia z efektem "wybłyszczenia" miejsc gdzie kontakt farby z folią był intensywniejszy.
- solerdmaski UV są znacznie bardziej miękkie niż te przeznaczone do wypalania